Table Of Content
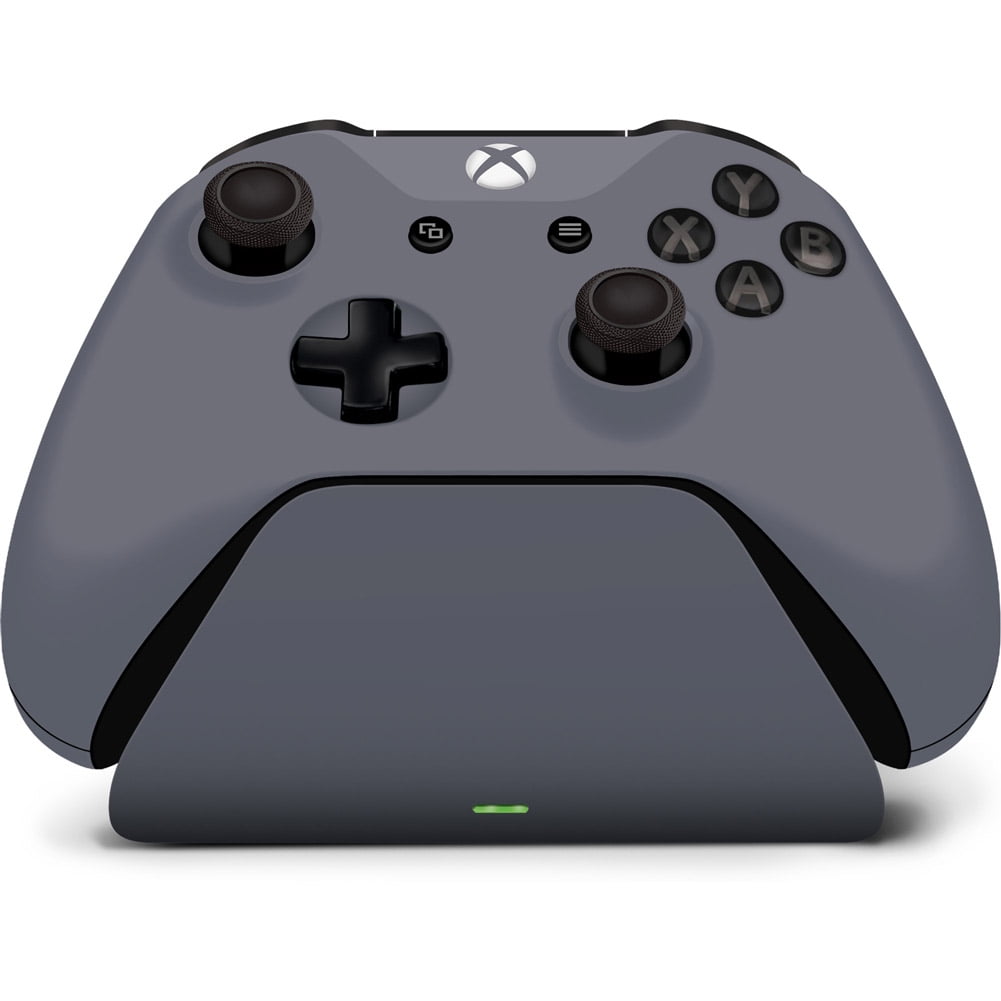
Recall that that design had more Percent Overshoot than expected, and a longer Settling Time, so let us look for an improvement. Remember that the first step is always to choose the required DC gain based on the error specs – the calculations are identical to the simplified method, so the Controller DC gain ([latex]a_0[/latex]) will be the same. We could try to improve on this design by trying a different choice of the crossover frequency. However, it is much easier to meet all conditions using the analytical design formulae, which we will try next. Simply "buying a textbook" on controls will help you get started, but the actual controller design is often much easier than understanding the plant and developing a decent model. Once you are satisfied with the design and you've met your requirements you may want to take the model and the controller into a simulation tool.

How To Factory Reset A Corsair Void Gaming Headset
Fast-forward to today, and we can see some variations on analog stick and button layouts. But in the broader sense, the DualShock’s design has been the blueprint that everyone has been following for the last two and a half decades. Pick nearly any modern controller, and you can trace its base design back to the original PlayStation’s. After it, there’s a whole bunch of controllers that just look like the PlayStation controller. And yes, we’ve still seen some controllers break from Sony’s overall shape, like the motion-controlled Wii remote.
General Tips for Designing a PID Controller
Online marketplaces and e-commerce platforms play a significant role in expanding the reach of game controllers, providing a convenient avenue for enthusiasts to explore and acquire these devices from the comfort of their homes. The seamless integration of online storefronts with global shipping services facilitates the international distribution of controllers, transcending geographical boundaries and connecting gamers worldwide. Efficient supply chain management and robust logistics partnerships are pivotal in ensuring timely and reliable delivery, meeting the demand for these innovative gaming peripherals. Central to the controller’s functionality is the PCB (printed circuit board), a vital component that serves as the platform for mounting and interconnecting the electronic elements. The PCB undergoes rigorous design and testing to accommodate the intricate network of sensors, buttons, triggers, and analog sticks, while maintaining optimal signal integrity and electrical efficiency.
Upgrade Your Hardware:
The arrangement of buttons, switches, and directional controls should prioritize ergonomics and intuitive access, enhancing your gaming performance and comfort. By meticulously wiring and soldering the components, you establish a robust electrical infrastructure within your custom game controller, laying the groundwork for reliable and responsive gameplay. The attention to detail in this phase ensures that your controller functions seamlessly, delivering the tactile feedback and precision required for an immersive gaming experience. Programming the microcontroller is a pivotal phase in the creation of a custom game controller, as it defines the behavior and functionality of the controller’s inputs and outputs. Whether you’re utilizing an Arduino, Raspberry Pi, or other programmable microcontroller, the programming stage empowers you to tailor the controller’s behavior to suit your gaming preferences and unique design features.
This panel packs a punch with high-quality trackballs and machined knobs for precise control over color correction. Whether you’re adjusting shadows, highlights, or saturation, the tactile feedback provided by these controls allows for nuanced fine-tuning. The analytical design gives us more flexibility to shape the open loop response by choosing different locations for the crossover frequency and quickly checking the resulting open loop parameters and the closed loop response. The step response of the closed-loop system (Figure 5.2.2) shows a 5% overshoot and a settling time of 11.5 sec. A controller for a sampled-data control system can be obtained by emulating (i.e., approximating) an available analog controller design. Controller emulation aims to obtain an approximate digital controller, \(K\left(z\right)\), whose response matches that of the analog controller, \(K\left(s\right)\) as measured by a selected metric.
In particular, the choice of closed-loop roots is restricted to those locations on the available root locus plot. An analysis of the closed-loop systems shows that all except the impulse invariance approximation are stable with damping in the range of \(\zeta \in [0.72,0.81]\). Wireless connectivity and communication protocols undergo stringent testing to validate seamless pairing, low-latency operation, and robust signal integrity. These assessments ensure that the controller delivers reliable and responsive wireless connectivity, empowering gamers with the freedom to play without constraints or interruptions.
Pics or it didn’t happen
Sony Access controller review: Sony gets accessible gaming almost right - Fast Company
Sony Access controller review: Sony gets accessible gaming almost right.
Posted: Mon, 04 Dec 2023 08:00:00 GMT [source]
And as you drag them you can observe your gain and phase margins from the open loop Bode plots, the closed loop bandwidth and modes from the closed loop Bode, and the rise time, overshoot and settling from the step response. Once you have selected and designed the layout of your custom game controller, the next crucial step is wiring and soldering the components to bring your design to life. This phase involves the meticulous connection of buttons, switches, directional controls, and the microcontroller, ensuring that each component functions seamlessly within the controller’s framework. Designing the layout of your custom game controller is a pivotal step that directly impacts the functionality and user experience.
Choosing the Right Components
The assembly process is a testament to the dedication and expertise of the manufacturing team, culminating in the creation of a game controller that embodies precision, reliability, and ergonomic excellence. With the controllers assembled, the next phase involves comprehensive testing and quality control measures to ensure that each device meets the exacting standards set forth by the manufacturer. Wireless connectivity features prominently in modern game controllers, with Bluetooth and proprietary wireless protocols enabling seamless pairing and low-latency communication with gaming platforms. Microcontrollers and specialized integrated circuits form the brain of the controller, orchestrating the interpretation of user input, the generation of haptic feedback, and the seamless communication with gaming consoles or PCs. These components are meticulously selected for their processing power, power efficiency, and compatibility with a diverse range of gaming platforms, ensuring broad accessibility for gamers. By meticulously selecting materials that prioritize durability, tactile comfort, and electrical performance, the production of a game controller achieves a harmonious fusion of form and function.
Iterate through various gaming scenarios to assess the responsiveness and compatibility of the controller across different game genres and applications. Ensure that the enclosure provides ample space for the internal components, allowing for secure mounting and cable management. The layout of the enclosure should accommodate the wiring paths and the placement of the microcontroller, buttons, switches, and directional controls, ensuring a snug and organized fit for the components.
Plus of the simplified design – it will never lead to negative values of the controller parameters, which may happen with the Analytical Lead Design. There are a whole lot of other things to consider such as noise sensitivity, disturbance rejection, robustness to plant perturbations, etc. Also the controller solution will need to be reduced to either analog (op-amp), discrete (computer controlled) or even mechanical elements. So you may need to decide things like sampling rates, which if not properly selected can lead to instability or degrade expected performance. It took me about 15 min to tune it to meet your specifications, but only because your specifications are pretty aggressive.
But after generations of experimentation, with different game companies all trying to solve the problem of “what makes a good controller,” nearly all of the successful controllers to date are based on Sony’s original design. The presence of a pole–zero pair adds a closed-loop system pole with a large time constant. The zero location can be adjusted so that the contribution of the slow mode to the overall system response stays small. Test the connectivity and communication between the controller and the gaming platform, whether it’s a PC, console, or mobile device. Ensure that wired or wireless connections are stable and that the controller is recognized and responsive within the gaming environment. Finally, integrate any additional features or embellishments, such as custom artwork, LED lighting, or engraved designs, to personalize the enclosure and make it uniquely yours.
Address any ergonomic or structural concerns to enhance the controller’s longevity and user experience. Leverage libraries and resources available within the programming ecosystem to expedite the development process. The method is ineffective if the analog controller has poles at the origin (as in the case of PI and PID controllers). The design was so successful that Sony has barely changed it four console generations later — and it looks like the upcoming PlayStation 5 will be following in the DualShock’s footsteps, too. Moreover, the packaging serves as an extension of the brand’s identity, featuring captivating graphics, iconic branding, and informative content that communicates the controller’s features and capabilities. The packaging design is a fusion of practicality and aesthetic appeal, featuring custom-molded inserts that cradle the controllers securely while presenting them in an engaging and visually striking manner.
These treatments not only enhance the visual appeal of the controller but also provide protection against wear and environmental factors, prolonging the lifespan of the enclosure. Soldering plays a pivotal role in establishing reliable electrical connections within the controller. Ensure that you have a well-ventilated workspace and the necessary safety equipment, such as eye protection and heat-resistant surfaces, before commencing the soldering process. Familiarize yourself with proper soldering techniques to achieve strong and durable connections without damaging the components.
No comments:
Post a Comment